New method 3D-prints metal foam for cheaper oil filters, noise isolation
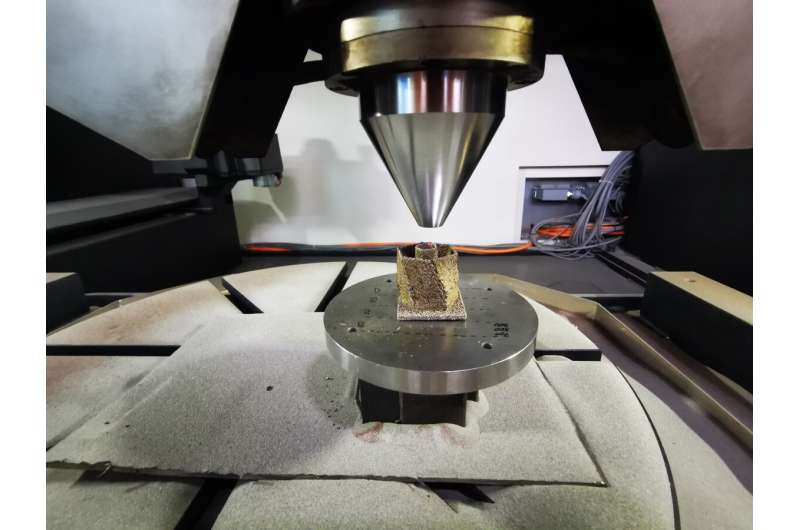
Skoltech researchers have devised a way to 3D-print metal foams. These materials are used in filters for purifying oil and gas, heat dissipators for effectively cooling the hot parts of an air conditioning system, and insulation for managing noise and vibrations in cars, aircraft, rockets, and other vehicles and industrial settings.
Described in the Journal of Porous Materials, the technique conserves raw materials, electrical power, and time, and cuts expenses. It even enables fine-tuning pore density and size to vary them from one spot in the manufactured part to another for meticulous control over the material’s properties.
Metal foams are a class of materials that look like a rigid sponge made of metal and have technologically appealing properties. They are lightweight, porous and have high compressive strength. Among other things, they are used to filter out impurities from crude oil and natural gas. This kind of material is also good for noise isolation and vibration damping, for example to enclose a ship’s engine room. The pores in the foam mean that it has an extremely high surface area per unit volume. It can therefore function as a very high-tech alternative to cooling fins—surface extension elements that carry heat away from a tube or other hot metal part, familiar from room heating radiators.
Traditionally, two approaches have been used to manufacture metal foam: hot pressing of metal powder and foaming of molten metal with inert gas bubbles. Now, a team of Skoltech researchers led by Assistant Professor Stanislav Evlashin of Skoltech materials—the principal investigator of the study—is proposing a promising alternative to those conventional methods to make the process way more efficient and customizable.
The first author of the study, Senior Engineer Oleg Dubinin of Skoltech Materials, explained the basic premise of what the research team refers to as direct metal foam printing, or DMFP: “Basically, we have adapted a 3D printing technique called direct energy deposition, which is normally used to print solid metal parts and deposit coatings, to metal foams. We have already shown this to work with titanium, aluminum, and an aluminum-bronze alloy, but experiments with other metals and alloys will follow. Importantly, no hardware modifications were required, so by merely tweaking certain software parameters, we extend the scope of what’s possible with 3D printing.”
The printing works in roughly the following way. The machine feeds metal powder in an inert gas flow into the zone where laser radiation heats the surfaces of the powder particles, fusing them to each other and to the substrate, resulting in metal foam formation. The key difference from the classical direct energy deposition process is a much lower laser power and a fine-tuned powder feed rate. A suitable combination of these and some other parameters makes it possible to print metal foam products on a conventional DED 3D printer.
According to the research, direct printing has a number of advantages over the traditional methods for making metal foam in terms of cost and efficiency.
Conventional techniques split up the manufacturing process into two stages. Depending on which method is used, you either need to make an ingot and then shape it by machine working or produce a mold and then cast or press the part in it. In any case, these additional stages consume extra time and raw materials. With direct metal foam printing, no tooling is required for manufacturing, no metal shavings are lost to postprocessing, and no additional machines besides the 3D printer itself are used to complete the entire process, which also cuts production costs.
The energy efficiency is high, too, owing to the very low laser power required—about 20 times lower than for direct deposition of solid metal parts.
Another advantage has to do with the proportion of pores in the foam that are open. 3D printing can achieve nearly 100% open porosity, which is crucial for filtration and heat management. Sealed-off pores do not permit liquid or gas to pass through, so they do not contribute to filtration. Neither do they encourage heat transfer where heat dissipation is the objective.
Unlike the conventional methods, which produce foam with more or less uniform porosity, direct metal foam printing enables an unprecedented degree of control over how pore size and pore density vary throughout the metal part that is being manufactured. For example, one might produce a filter that gradually goes from larger to smaller pores, responsible for different kinds of impurities.
Even the chemical composition of the material can be varied in a similar manner. For instance, the foam serving to draw heat away from a tube exposed to extremely high temperature might be made of titanium where it touches the tube to withstand that harsh environment. But as it gets farther away from the tube, the alloy constituting the metal foam might shift its composition in favor of aluminum. That metal has a better thermal conductivity and would be better-suited for giving off that heat to the environment.
More information:
O. N. Dubinin et al, A promising approach to 3D printing of metal foam with defined porosity, Journal of Porous Materials (2023). DOI: 10.1007/s10934-023-01440-4
Citation:
New method 3D-prints metal foam for cheaper oil filters, noise isolation (2023, April 26)
retrieved 26 April 2023
from https://techxplore.com/news/2023-04-method-3d-prints-metal-foam-cheaper.html
This document is subject to copyright. Apart from any fair dealing for the purpose of private study or research, no
part may be reproduced without the written permission. The content is provided for information purposes only.
For all the latest Technology News Click Here
For the latest news and updates, follow us on Google News.