Combining 3D printing and sensors for safer, cheaper flying
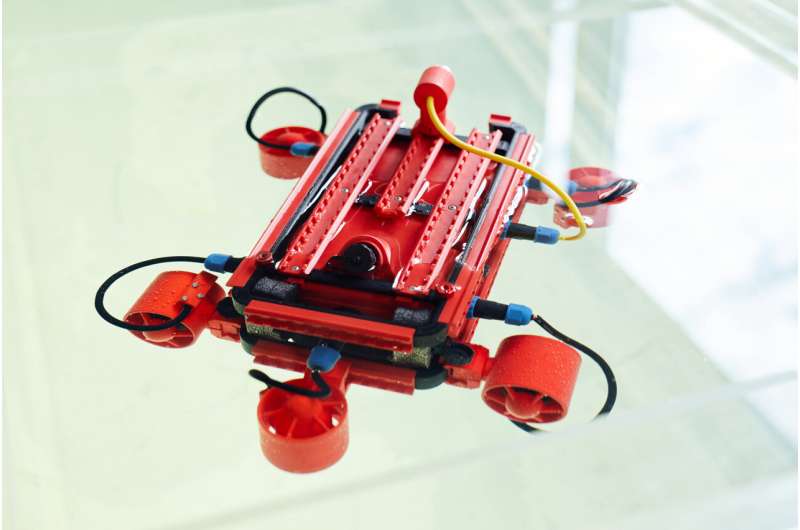
The aeronautical industry has transitioned to the use of advanced composite materials because of their lightweight properties, strength and durability. Together with increased aircraft productivity and performance, using these advanced materials makes designing and manufacturing cost-effective aircraft structures and components more challenging. Meeting these challenges will lead to a reduction in weight and fuel consumption, shorter manufacturing cycles and increased energy efficiency in aircraft assembly.
Nowadays, many aircraft parts are 3D-printed composites. Embedding carbon nanotubes (CNTs) during the manufacturing process of components is very suited to overall workflow. Embedded sensors are ideal for high-value and critical aircraft components or procedures. For such components, 3D printing can provide a cost-efficient means to making and embedding integrated sensor packages.
Researchers supported by the DOMMINIO project are developing embedded sensors that enable real-time monitoring of aircraft while in flight. The 3D-printed parts embedded with CNT fibers generate data that can then be used for monitoring the part. This could reduce assembly costs and limit the need to use many wires to connect the sensors together.
Better predictive maintenance
“The sensors are being designed to be made from these fibers, which are incredibly light compared to existing materials and which also consume very little energy,” states Dr. Moisés Zarzoso, a research assistant at project partner IMDEA Materials Institute, Spain, in a news item posted on “3DPrint.com.” “They are also 3D-printable and, given that they are CNT fibers, they can be easily embedded into a component manufactured from traditional carbon fiber, which is a very common material in aircraft production.”
A major aspect of the project is the use of digital twins. Dr. Zarzoso explains, “They are called digital twins because they are very accurate digital models that are updated during the whole life cycle, replicating the physical part or component within the aircraft in real-time. Through its embedded sensor, the physical part is able to communicate directly with engineers on the ground. If, for example, you had an impact during flight from hailstones, information relating to any possible damage to the part would be recorded by that sensor and then sent automatically to its digital twin. Using that information, the simulations that we are developing will be able to analyze the risk that a potential impact could induce in the structural integrity of the component, and to determine its remaining lifespan.”
The 3D printed aircraft sensors can help to save costs in several ways. These include more precise maintenance intermissions, flagging issues before they cause flight delays, and the checking and analytics of components.
The DOMMINIO (Digital method for imprOved Manufacturing of next-generation MultIfuNctIOnal airframe parts) project is developing a novel digital methodology for the design, manufacture and certification of multifunctional and intelligent airframe parts. It ends in June 2024.
Developing next-gen, smart engine fan blades
Citation:
Combining 3D printing and sensors for safer, cheaper flying (2022, October 3)
retrieved 3 October 2022
from https://techxplore.com/news/2022-10-combining-3d-sensors-safer-cheaper.html
This document is subject to copyright. Apart from any fair dealing for the purpose of private study or research, no
part may be reproduced without the written permission. The content is provided for information purposes only.
For all the latest Technology News Click Here
For the latest news and updates, follow us on Google News.