Versatile porous flexible sensor prepared by photocurable 3D printed ionogel
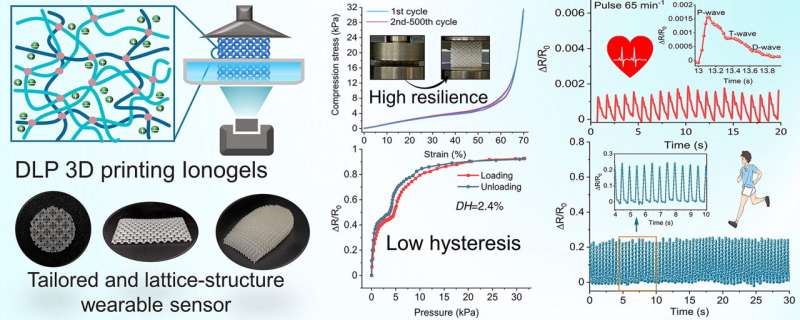
Flexible sensors are widely used in health diagnosis, motion monitoring, and human-computer interaction due to their excellent tensile properties, electrical conductivity and fit.
However, due to the inherent viscoelasticity of soft materials, the flexible sensor cannot quickly recover its original shape during dynamic loading, resulting in a large hysteresis in the signal of the flexible sensor, which seriously affects the monitoring accuracy of the flexible sensor. How to quickly and accurately fabricate flexible sensors with low hysteresis remains a challenge.
In a study published in the Chemical Engineering Journal, the research group led by Prof. Wu Lixin from Fujian Institute of Research on the Structure of Matter (FJIRSM) of the Chinese Academy of Sciences, developed a high resilience, low hysteresis and versatile porous flexible sensor by photocurable 3D printed ionogel.
Based on hydrogen bond-rich acrylate monomers and ionic liquids, the researchers prepared a photosensitive resin with fast polymerization rate for digital light processing (DLP) printing of porous ionogel flexible sensors (PIFS), and a deformable Alan Schoen’s I-wrapped package (IWP) lattice was introduced in PIFS to improve the resilience of the flexible sensor.
The experimental results showed that after 500 cyclic compressions with a strain of 70%, the residual strain of the lattice-structured PIFS is almost 0, and the hysteresis loops are almost overlapped, showing that the PIFS has excellent resilience and fatigue resistance. High elasticity and durability enable PIFS to have low hysteresis (2.4%), providing reliable sensing signals during long-term cyclic loading. The introduction of lattice structure also makes PIFS have higher pressure sensitivity (0.45 kPa-1).
The researchers also took advantage of the freely designable structure of 3D printing technology to design and print PIFS with customized structures for monitoring pulse, finger, gait and wrist movements.
In addition, PIFS has a low glass transition temperature (-45.8 degrees Celsius) and can work stably in a low temperature environment. It also has antibacterial properties and rapid response to temperature changes, which can monitor temperature changes, demonstrating that PIFS is a versatile flexible sensor.
This study solves the hysteresis problem of flexible sensors by designing lattice structures in the sensor using 3D printing technology.
Novel double helix yarn piezoresistive sensor for pulse monitoring
Shuqiang Peng et al, Tailoring of photocurable ionogel toward high resilience and low hysteresis 3D printed versatile porous flexible sensor, Chemical Engineering Journal (2022). DOI: 10.1016/j.cej.2022.135593
Citation:
Versatile porous flexible sensor prepared by photocurable 3D printed ionogel (2022, May 9)
retrieved 9 May 2022
from https://techxplore.com/news/2022-05-versatile-porous-flexible-sensor-photocurable.html
This document is subject to copyright. Apart from any fair dealing for the purpose of private study or research, no
part may be reproduced without the written permission. The content is provided for information purposes only.
For all the latest Technology News Click Here
For the latest news and updates, follow us on Google News.