‘Secret sauce’ enables new way to fabricate compositionally graded alloys
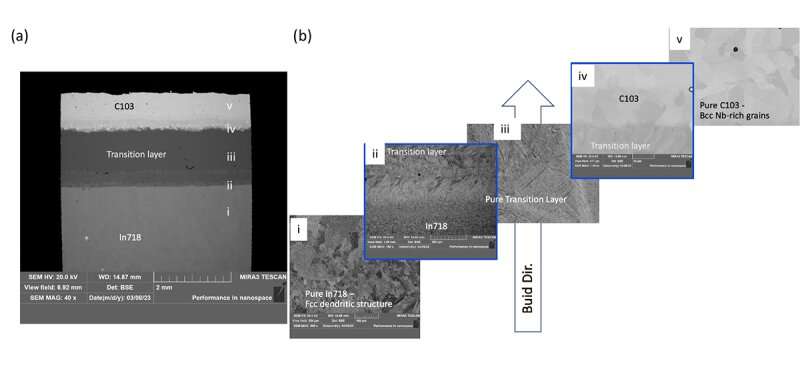
Research into a new, unique technology to fabricate composite metal parts for a wide range of applications operating in extreme environments across the aviation, space and energy industries is showing promise for additive manufacturing.
Developed by scientists at the Department of Energy’s Oak Ridge National Laboratory, this technique enables design of compositionally graded composite parts. These components transition from high-strength superalloys to refractory alloys that can withstand extremely high temperatures—so no welding is needed.
Though superalloys and refractory alloys typically cannot be welded or joined with each other, many applications require materials with site-specific high-temperature and high-strength properties.
“We can enable compositions that transition from one alloy to another seamlessly,” said Soumya Nag, an ORNL materials scientist who is leading the studies. “We can tune a composite part that we can grade from one end to another and have high-strength and high-temperature capability on each side.”
The secret is in the “sauce.”
“It’s like cooking. You basically have different ingredients. So, if you have more pasta on one side and more risotto on the other side, how do you continuously change from a pasta to a risotto? You change the ingredients as you move along from one end to another, and that’s exactly what we do,” Nag said.
The sauce in this case is a powder composed of a third transition alloy that possesses lightweight or high-temperature characteristics. Nag and team members used an additive manufacturing modality called directed energy deposition to deposit different powder compositions in an inert argon environment, changing the deposition rate as they go along.
For most structural applications, Nag said, a single alloy composition is often used to fabricate components for corrosive, high-temperature or radiative environments, but this process is expensive and compromises performance. For components requiring widely varied properties, welded parts made from dissimilar materials are often fabricated, leading to abrupt interfaces that can adversely impact performance.
In the latest studies, the scientists used powders of Inconel 718, a nickel-based alloy, and C103, a niobium-based alloy. These alloys—one high strength and the other high-temperature resistant—do not want to join and tend to create cracks when they do. But by using a blown-powder directed energy deposition beam machine and changing the rate at which the powders flow, the scientists can change the composition of the joined metals so that it has the beneficial properties of both.
The scientists designed the actual non-linear gradient pathway by coupling state-of-the-art computational thermodynamics with experimental data gathered via multiscale, high throughput characterization tools. By doing so, they successfully circumvented welding issues and joined normally nonweldable superalloys with refractory alloys.
The team analyzed the stress states of these integrated builds with neutron diffraction-based studies at ORNL, validating the computational alloy design. Currently, melt pool, thermal and strain models are being generated based on the experimental data.
“Few additive manufacturing modalities have this capability of mixing powders on the go during the build,” Nag said. “This is a unique attribute that can blow powders at different rates. Now you can do temperature transition from a relatively low-temperature nickel alloy to an extremely high-temperature niobium alloy without any problem.”
Among the applications for this technology are rocket engines for space, aerospace manufacturing, fusion and fission reactor fabrication, marine-related uses, renewable energy systems—anywhere an extreme environment exists, Nag said.
“We are driving toward a future where customized components with an ideal combination of component-specific performance with reduced fabrication cost may be incorporated for a wide range of applications,” he said. “It could change the way components for extreme conditions are made.”
Nag has filed a provisional patent application involving the materials employed and the manufacturing process. Contributing to the research are ORNL scientists Brian Jordan, Ke An, James Haley, Yousub Lee and Jaimie Tiley. Truly cross-disciplinary, the research team members from across ORNL bring expertise in physical sciences, energy science and technology, neutron sciences and computing and computational sciences.
Citation:
‘Secret sauce’ enables new way to fabricate compositionally graded alloys (2023, July 21)
retrieved 21 July 2023
from https://techxplore.com/news/2023-07-secret-sauce-enables-fabricate-compositionally.html
This document is subject to copyright. Apart from any fair dealing for the purpose of private study or research, no
part may be reproduced without the written permission. The content is provided for information purposes only.
For all the latest Technology News Click Here
For the latest news and updates, follow us on Google News.